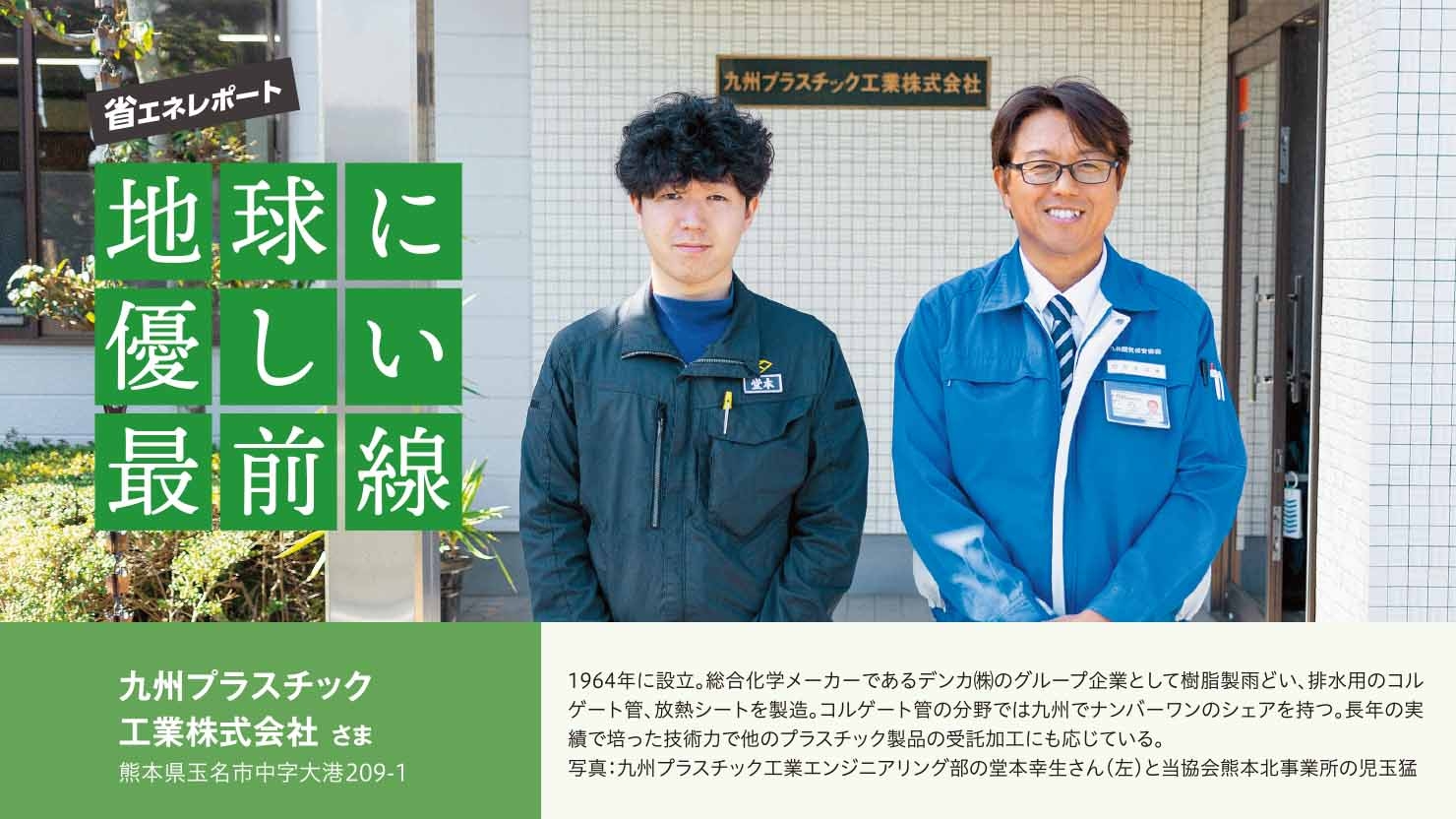
省エネレポート
九州プラスチック工業株式会社 さま
電気の使い過ぎを突き詰める
九州電気保安協会では省エネに取り組む企業や施設の皆さまをサポートしています。
今回ご紹介するのは、合成樹脂の加工・成型を手がける九州プラスチック工業株式会社さま。
エンジニアリング部・堂本幸生さんに、節電について語っていただきました。
ECOねっとシステムで電気を監視
アクリル樹脂やポリ塩化ビニルなどのプラスチック製品を製造する当社の工場には、電熱ヒーターや電動モーターを多用した成型機が14機あります。とても大きな電力を消費するので、10年ほど前からデマンド管理による節電を心がけています。当初の監視装置は社屋外の受電設備小屋にあったため、電気担当者が事務所から小屋に何度も往復して数値を見ていました。また使用電力の記録は紙への印刷。その整理が負担でもあったので2018年にECOねっとシステムを導入しました。年・月・日単位の電力使用データを配信してくれるので大変便利。ECOモニターは事務所とエンジニアリング部に設置し、さらに私たちのアイデアで、モニターを写すWebカメラを天井に取り付けているので、いつでもどこでも自宅にいてもスマホ画面でモニターの数値を確認できます。
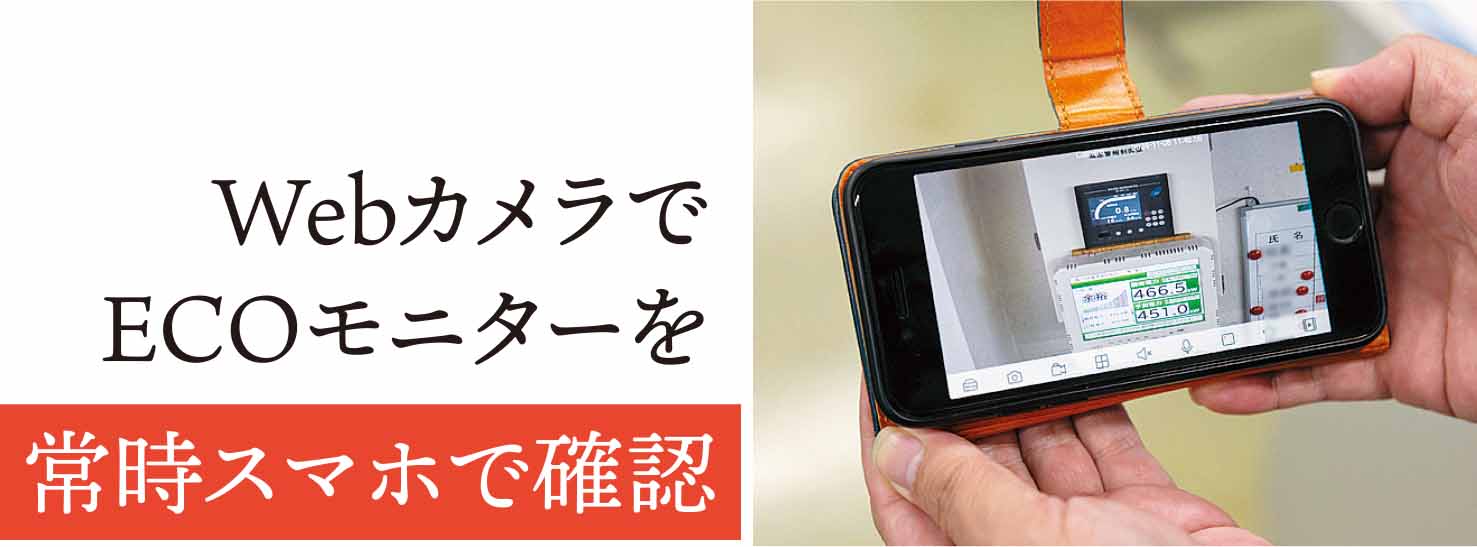
緊急停止可能な機器リスト
まず私たちが行ったのは、工場の製造機器や空調など個々の消費電力を測定したリストの作成。これを製造計画に落とし込んでデマンド危険日を予測した製造計画表を作成します。契約電力は930kWで、総電力830kWを基準にして「慢性的に基準値を大きく超える可能性が高い日」「電力ピーク時に基準値を超える可能性が高い日」などと色分けして、製造部門に注意を促します。しかし、予測に反して危険日でなくてもデマンドを超えそうになることもあります。瞬間電力が1,000kWを超えたことも。警告が鳴ったら速やかに各部署の責任者に連絡。あらかじめ作成した緊急停止可能な機器リストを基に停止してもらい、30分デマンドをクリアします。樹脂の製造現場では最も消費電力が大きい成型機など、緊急停止できない機器が多く、それが悩ましいところです。
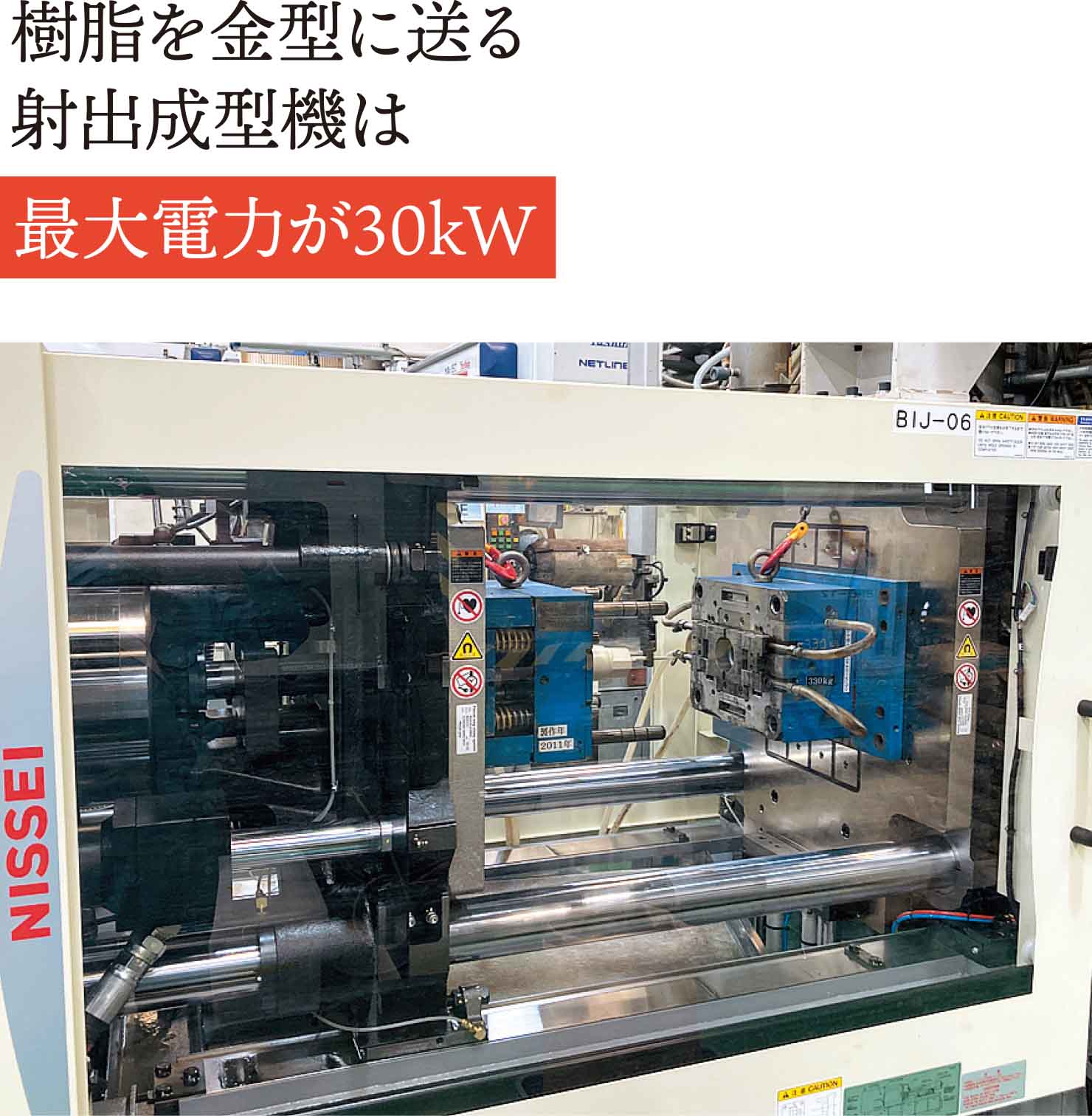
930kWの契約電力を維持
デマンドを上げない工夫は他にもあります。電動フォークリフトの充電は、電力使用が少ない夜間にまとめて行います。ただ、夜間充電をうっかり忘れたり、朝から稼働して昼にはバッテリーが切れて再充電する場合があったりするので油断できません。起動時に最大電力を使う空調機器は、タイマー設定にして出勤時の起動時間を少しずつずらし、負荷が集中しないようにしています。
このような取り組みを7年間続けて現在にいたっていますが、この間に契約電力を超えたデマンドを出したことは一度もなく、毎年の平均最大デマンドは781~866kWに収まっています。この7年間で製造機器を増やすなど設備投資をしているので電力量は増えて当然なのに、930kWの契約電力を維持できています。コンスタントにかなりの節電ができていると思います。
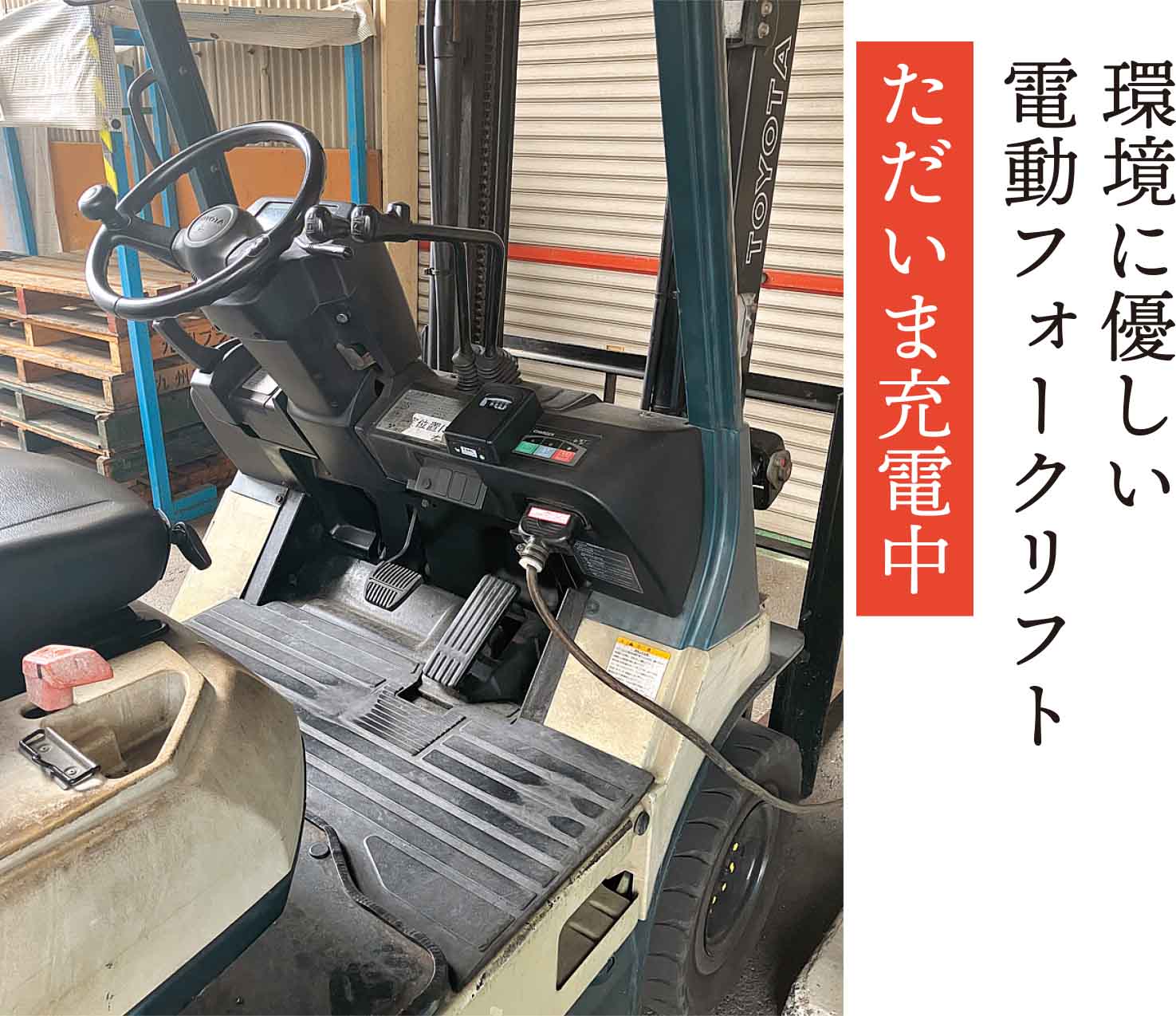
データから無駄な電気を発見
機器の省エネ化も進めています。受電設備のトランスは省エネタイプに更新。成型機やコンプレッサーなどはインバーター化・ハイブリッド化しています。樹脂を溶かす加熱ユニットも高効率なものに。照明のLED化は随時進めており、トイレ・更衣室などの照明は人感センサーで電気の浪費を防止しています。
デマンド管理とは別の話ですが、製造のラインごとに製造高と電力量を月単位で記録し、その推移をグラフにしています。製造高と電力量は比例するのが正常ですが、製造高が減っているのに電力量が上がっている月があったりする。そんなときは「えっ、何で?何で?」と電気を使い過ぎた原因を徹底的に追究します。測定したデータを集めて、それを比較検討することで、それまで見えなかった無駄な電気を発見することがあるのです。
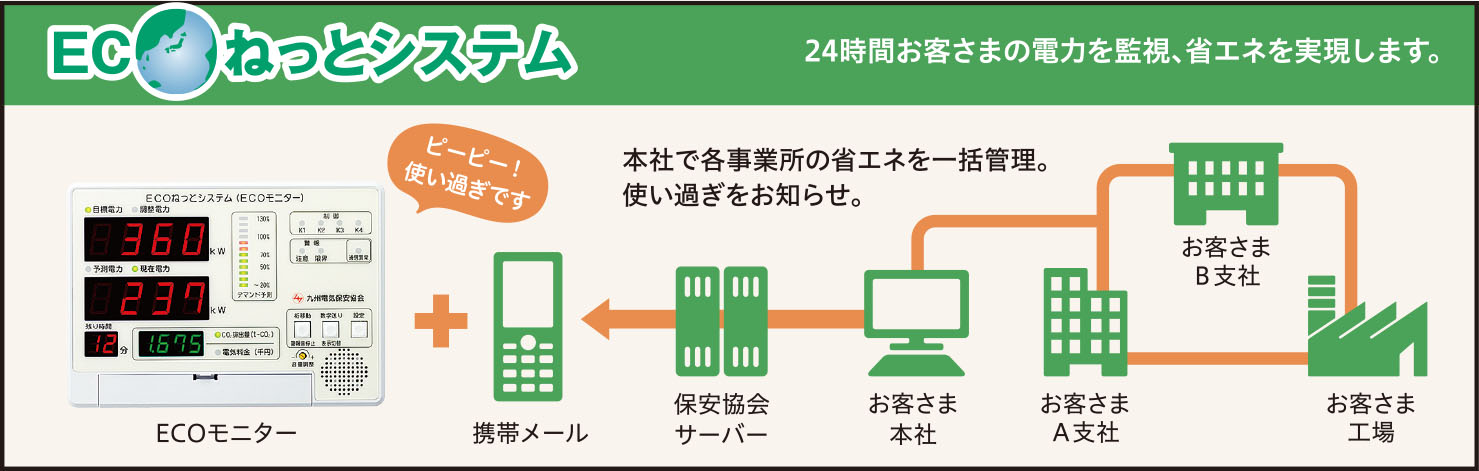